Considerations When Selecting an Alloy or Material
September 27, 2023
on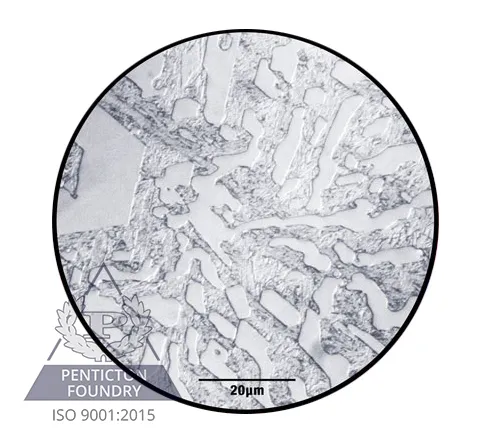
Knowing how to choose a material or alloy for a given application is critical in ensuring that the resulting casting or product meets expectations. In order to select appropriately, an understanding of the application’s requirements, as well as the properties of available alloys or materials is needed. This blog offers tips to help engineers make the right choice.
Tips For Alloy/Material Selection
1) If possible have a materials engineer and designer work together
- The designer will outline the operation of the component
- The designer will also describe the functionality required
- At this point constraints on the part should be considered
2) Consider material properties
- A primary consideration when choosing an alloy or material is the material properties, as their combination will define the performance of the part
- Material properties are as follows: mechanical, physical, optical, electrical, thermal, and magnetic
- Within this list of material properties, it is mechanical properties that play the greatest role in alloy selection
- Measurements like ultimate tensile strength, yield strength, ductility, hardness, fatigue strength, and impact resistance are some of the key mechanical properties
- Most mechanical properties are documented for alloys, and understood by the design team
- For example, the ASTM A536 standard clearly outlines the ultimate tensile strength, the yield strength, and the elongation that a ductile iron casting will possess. The design team will understand how to use these values, but also understand their limitations. For example, a possible overload to a part should not exceed the yield strength, or failure could ensue
Read: To read about several different ductile iron alloys and their mechanical/physical properties, check out all of our ductile iron data sheets.
3) Consider the manufacturability of the part
- Manufacturing considerations are: material factors, process factors, shape factors and fabrication factors
- The material factors will define limitations on how a part can be processed. For example, an alloy with an extremely high melting point may not be the best choice for a casting, or an alloy that cannot be plastically deformed would not be a good choice for a forging
- The process factors that are important to manufacturing are: cycle time, quality, flexibility, materials utilization, and operating cost
- The shape of the desired product, i.e. the shape factor, is critical in assessing the manufacturability of the part. For example, if it is a complicated shape, with different section thicknesses, perhaps consider a casting rather than a fabrication
- Fabrication factors are also referred to as the ease of manufacturing
- These processes are: workability, castability, machinability, weldability and heat treatability
Read: To take a closer look at casting vs fabrication read this blog.
4) Conduct a Cost Assessment
- A good team of designers and materials engineers will consider the total cost of ownership, as well as the lifespan of the product
- Material choice is impacted by the potential degradation (corrosion or erosion) of a part during service
- For example, a wear part may be built with AR plate because it is inexpensive, and changeout is also inexpensive, but if a part made in high chrome white iron is twice the price of a part made in AR plate, but will last 6 times longer, the choice to use high chrome white iron may be the correct one
Read: This case study explores how chrome white iron outlasted AR400 in a mining application. The visuals are quite impactful.
Resource: To learn more about re-shoring and total cost of ownership, read this resource.
5) Availability of material
- How readily available is the material of choice? If it is difficult to source the material requested, perhaps an alternate should be used
6) Stability during lifespan
- Some parts will be subjected to temperature changes or fluctuations, and/or extreme temperatures (both hot and cold)
- Some parts may also be exposed to radiation
- These influences will affect the choice of material for some applications
Read: To learn more about the different mechanical and physical properties of various chrome white iron alloys, take a look at our chrome white iron webpage. To access all of our gray iron data sheets, which include composition notes and mechanical/physical properties, check out our gray iron webpage.