Heat Resistant Gray Iron ASTM A319
on April 12, 2022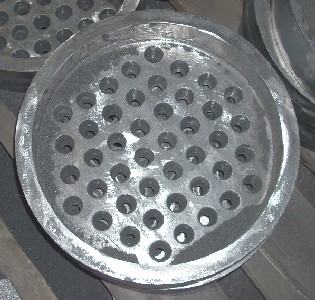
Heat resistant gray iron is used for castings that experience temperatures up to 1400 F. ASTM A319 has resistance to growth and oxidation, resistance to thermal shock, response to cycling heat and high temperature fatigue strength.
There are three different classes of heat resistant gray iron that are used for different temperatures and applications.
Class I: Best resistance to thermal shock
Class II: Average resistance to thermal shock and tensile strengths above 30000 psi
Class III: Highest tensile strength
Heat resistant gray irons are classified by their Carbon Content Equivalent (CE):
Class | CE |
I | 3.81 – 4.40 |
II | 3.51 – 4.10 |
III | 3.20 – 3.80 |
The three classes can then be alloyed with chromium and sub-divided into types:
Type | Cr % |
A | 0.2 – 0.4 |
B | 0.41 – 0.65 |
C | 0.66 – 0.95 |
D | 0.96 – 1.20 |
The purchaser and manufacturer will agree on the grade of cast iron required for the desired application, as well as any additional alloying elements such as silicon, copper, molybdenum, nickel, and vanadium.
Read: To learn how gray iron and ductile iron compare read “Ductile Iron Versus Gray Iron Castings.”
Physical and Mechanical Properties
The chart below has a wide range of values based on how the material is alloyed.
UTS-ultimate tensile strength MPa (Ksi) | 170 – 620 (20 – 90) |
Hardness (HB) | 170 – 350 |
Compressive Strength MPa (Ksi) | 480 – 1100 (70 – 160) |
Impact Energy J (Ftlbf) | 20 – 200 (15 – 150) |
Transverse Breaking Load kg (lb) | 455 – 1590 (1000 – 3000) |
Transverse Deflection mm (in) | 1.5 – 35 (0.06 – 1.4) |
Applications
- Grate bars
- Stoker links
- Ingot molds
- Glass molds
- Aluminum smelting parts – like syphon tubes
Read: To learn more about gray iron check out our gray iron webpage.