The Differences Between Ductile Iron and Gray Iron Castings
on June 18, 2015Gray iron and ductile iron are differentiated by the type and structure of the carbon present in them. The question, of course, is which one is right for your project? Before we look at possible answers, let’s examine some of the key differences between the two cast irons. For a quick summary, scroll down to the bottom of the blog and check out our chart.
Key Differences
- Ductility – Ductility is determined by a greater percentage of elongation under tension. The addition of magnesium in ductile iron means that the graphite has a nodular/spherical shape conferring higher strength and ductility as opposed to gray iron which is flake shaped. For example, 18% elongation can be easily achieved with ASTM A395 and A536 grades 60-40-18 material.
- Tensile and Yield Strength – There are certainly differences when it comes to tensile and yield strength of gray and ductile iron. Ductile iron has a minimum tensile strength of 60,000 psi and a minimum yield strength of 40,000 psi. There are many grades of gray iron as per the ASTM A48 standard. While gray iron does not have a measurable yield strength, the range for tensile strength is 20,000 psi – 60,000 psi.
- Impact – Impact strength, also known as toughness, is a measure of a metal’s ability to resist fracturing while absorbing an impact (collision). Ductile iron has a greater resistance to impacts, and is able to resist a minimum of 7 foot pounds of impact (versus 2 pounds of impact for gray iron). This means that while ductile iron can be used in critical applications that involve impact, gray iron has limits that prohibit it from being used for certain purposes.
- Thermal Conductivity – Ductile iron has a lower thermal conductivity than gray iron. Specifically, the graphite phase in gray iron gives it very high thermal conductivity as the heat transfer is through the graphite flakes. The isolated spheres of graphite in ductile iron lower its thermal conductivity considerably – in fact it is not much more conductive than steel. As the amount of carbon increases, the thermal conductivity increases. This means that lower strength gray irons will have higher thermal conductivity. The design engineer needs to keep this in mind if the primary reason for choosing gray iron is for thermal conductivity. Gray iron, with its high thermal conductivity, is a great choice for parts that undergo thermal shock, like brake drums.
- Vibration Damping – Internal friction is how materials absorb vibrational energy. Gray iron dampens vibrations more effectively than ductile iron because gray iron exhibits non-elastic behavior at very low stresses. A higher damping capacity enhances fatigue resistance because the time duration when stress is at or above the fatigue limit is reduced. This enhancement of fatigue resistance is the most beneficial aspect of higher damping capacity. The other major benefit is the reduction of vibrations and noise that can be emitted by components of machinery.
We have included a chart comparing the two irons across a variety of factors. The checkmark in the appropriate column indicates the better choice between the two.
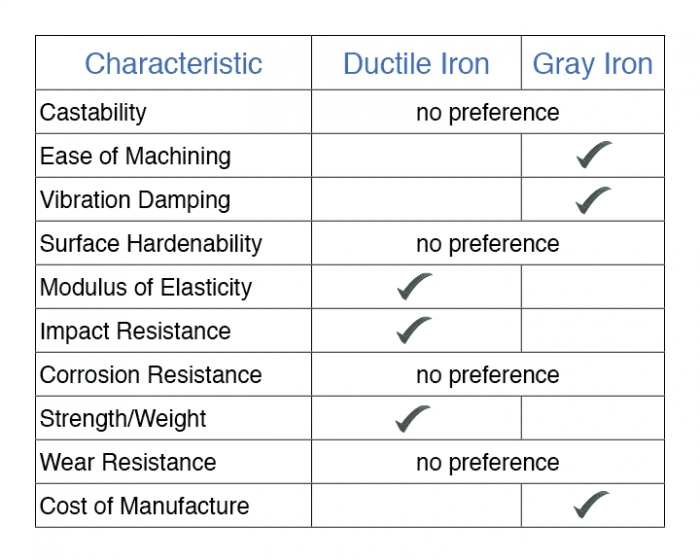