Why It Makes Sense to Use Chrome White Iron in the Oil Sands
on July 31, 2018Sometimes, you get a success story that helps illustrate why many companies are shifting to chrome white iron in abrasion applications. But what are the challenges that are specific to the Oil Sands, and what is it about chrome white iron that makes it so effective there?
Challenges in the Oil Sands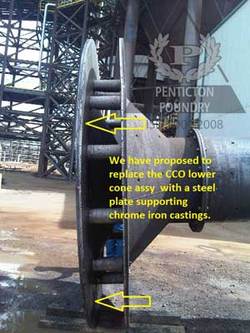
There are some challenges that are specific to the Oil Sands that make ASTM A532, high chrome white iron, highly suitable as a solution:
- Dense, abrasive media flows at a high velocity through the various pipes and vessels of the processing/refining process
- Pipe/vessel walls are constantly exposed to abrasion and impact – leading to an increased wear rate for components
- High costs associated with downtime and repair/replacement of worn components
Read: This article, complete with a chart from the National Resource Council, does a little myth busting. Specifically, there is a myth that chrome white iron is brittle.
How Chrome White Iron Addresses the Challenges of the Oil Sands
- The chemical composition – specifically the carbides in the matrix – of ASTM A532 or chrome white iron, create its superior abrasion resistance
- This makes it an excellent solution for lining parts or assemblies that need to withstand constant wear
- Piping assemblies, for example, can be lined with chrome white iron to conform to ASME B31.3 or ASME B31.4 specifications
- Very few modifications need to be done to the vessel or area to be lined (and in some cases none at all). This leads to significant cost savings as the casting is built to conform to the vessel or pipe’s shape
- Increased uptime of the wear part – chrome white iron can be cast to greater thicknesses than other common wear solutions such as CCO
- Decreased downtime leads to cost savings
To learn more about chrome white iron, check out our chrome white iron webpage.
Hydro Transport Pipelines and ASTM A532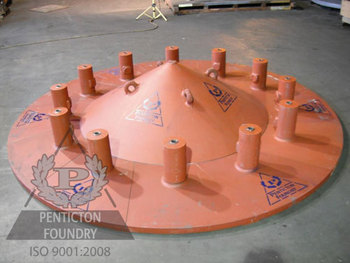
Hydro transport pipelines take the Oil Sands’ deposits (combined with water to make slurry which flows better along the pipeline) from ore preparation to the main extraction facility.
- As the media flows along the pipe and comes into contact with the pipe walls and adjacent media, it begins to break down. This is an advantage of the hydro transport process as it helps to free the bitumen deposits
- Unfortunately, it also causes the lines to wear as the abrasive media is traveling through the hydro transport lines at high velocity
- Combining chrome white iron with a secure pressure boundary is an innovative solution that successfully extends wear life
- In fact, chrome white iron lined hydro transport lines in the Alberta Oil Sands have lasted longer than other CCO equivalents
Design Tip – It is feasible to design spools to have separate castings at high wear areas (such as leading edges) that can be replaced without having to replace the entire spool liner
Watch: There is a myth that chrome white iron cannot be machined, but this video shows otherwise.
Conclusion
The chemical composition of chrome white iron, specifically the carbides in the matrix, make it a preferred material in the highly abrasive Oil Sands environment. Using chrome white iron can lead to a significant increase in the wear life of parts, and a subsequent decrease in downtime costs. Chrome white iron can be machined, and used as a viable replacement for CCO and AR plate in a number of Oil Sands applications.