Select the Best Alloy for Flue Gas Desulfurization
April 5, 2023
onWhat is Flue Gas Desulfurization?
In processes that produce a combustion exhaust gas, flue gas desulfurization (FGD) is used to remove the sulfur dioxide (SO2) before it enters the environment. There are both dry and wet flue gas desulfurization systems. In wet FGD systems the environment is very corrosive and can cause equipment to corrode and fail quickly. “Approximately 85% of the flue gas desulfurization units installed in the US are wet scrubbers, 12% are spray dry systems, and 3% are dry injection systems.”1 This article will focus on wet FGD systems.
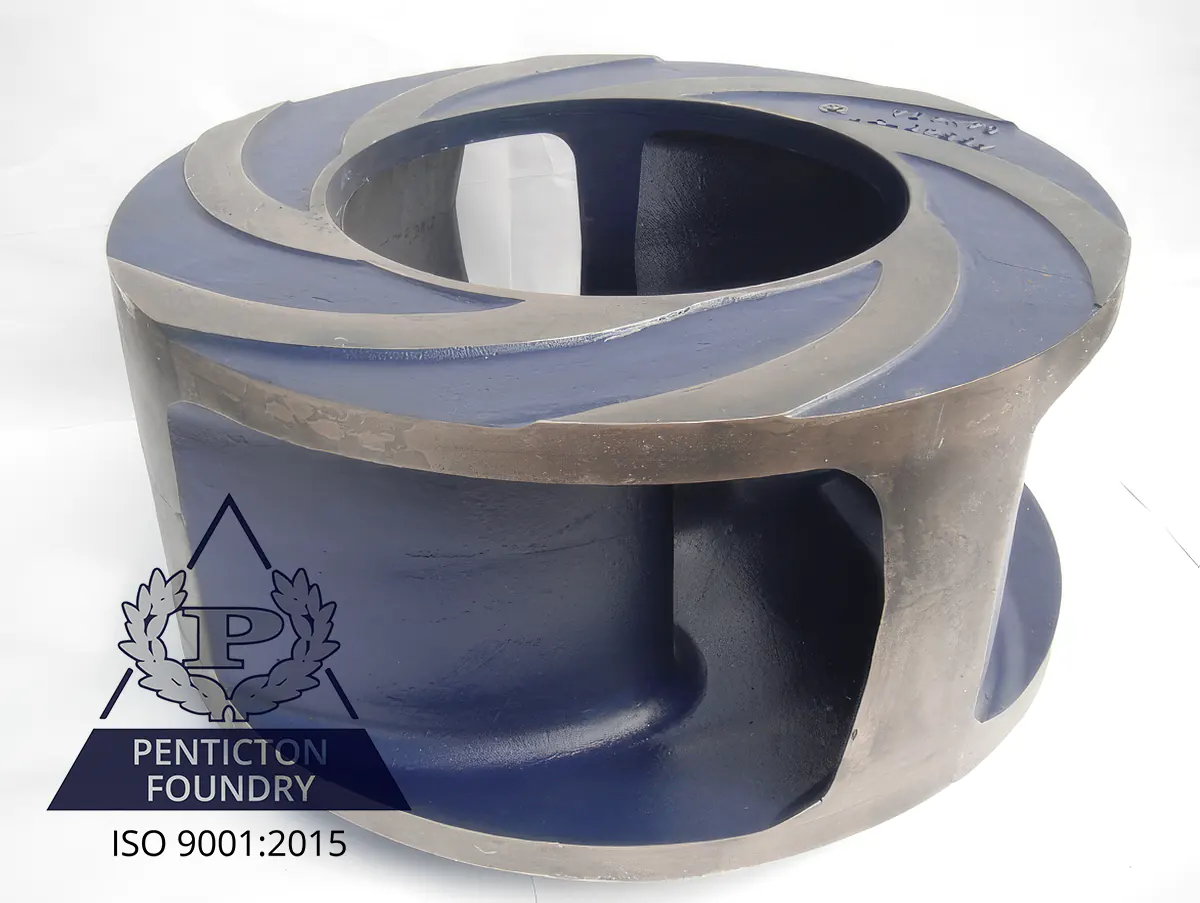
Industries that Use Flue Gas Desulfurization
There are a number of industries that use flue gas desulfurization to remove SO2 gases before they are released into the air. These include:
- Fossil fuel power plants – coal and other hydrocarbons
- Cement and lime kilns
- Chemical manufacturing
- Waste incineration
- Petroleum refineries
Challenges Associated with Flue Gas Desulfurization
- High capital costs
- Operation and maintenance costs
- Wet FGD systems - Deposit of wet solids on downstream equipment
- Wet FGD systems - Subsequent corrosion of downstream equipment –including abrasive wear in expansion joints
- Unplanned outages
Solutions
In wet flue gas desulfurization systems, gas saturated with water travels throughout the system and corrodes downstream equipment. There are 2 ways to fix this, either reheat gases to above their dew point, or design with materials that are able to tolerate the corrosive environment.
We will focus on the second of the 2 solutions:
Due to the many variables unique to each system (pH levels, chloride concentration, etc.) it is important to review the entire FGD system before deciding on the correct materials to prevent corrosion.
-
Although a tool for seawater applications, a quick review of the Pitting Resistance Equivalent number (PREn) may be used to compare different materials. The calculation can predict a material’s resistance to localized pitting corrosion using the material’s chemical composition. The higher the PREn, the less likely the material will be to corrode.
PREn=%Cr + 3.3 * %Mo + 16 * %N
Material PREn SS316L 23 SS317L 29 2205 Duplex SS 33-35 SS904L 35 30% Cr White Iron 34-35 Some things that will vary between materials include cost, deposit production, fabrication methods, contaminants, and additives.
- Cr-Mo Alloyed Steels
- Prevents corrosion because a thin, passive oxide layer forms containing chromium. This happens as soon as the material touches air
- Need to be careful as high temperatures can cause stress corrosion cracking in steels
- pH and chloride content in the system can create a pitting corrosion
- 30% Chrome White Iron
- Chrome carbides in the material act as corrosion prevention. The corrosive/abrasive performance is determined by microstructure and hardness, and is not dependent on the passive film
- Because the iron does not need to form a passive film over its surface, it is more likely to be resistant to stress corrosion cracking
- 30% Cr iron has been successfully used in environments with a pH level of 3. If temperature and chlorides are high, consider only allowing a pH of 4
- Cr-Mo Alloyed Steels
Note: 30% Cr white iron typically provides equivalent (or sometimes better) corrosion properties at a lower price point than steel or stainless steel.
Read: Our chrome white iron page contains links to all of our chrome white iron datasheets.
1 "Air Pollution Control Technology Fact Sheet: Flue Gas Desulfurization" (PDF). Clean Air Technology Center. EPA. 2003. EPA 452/F-03-034.