Ductile Iron vs Steel
on November 5, 2015Which Alloy is Better? Ductile Iron vs Steel
As we’ve already compared ductile iron castings to gray iron castings we thought we’d compare ductile iron and cast steel across a variety of properties to help determine which alloy is better for a given application. This blog is a simple, generic overview. We’ll take a look at tensile strength, ability to absorb shock, weldability, abrasion resistance and corrosion resistance.
Note: Ductile iron with its carbon content of 3.0%-3.9% has a higher carbon content than cast steel which normally has a carbon content of 0.08%-0.60%.
Tensile Strength
While there is no large difference when it comes to tensile strength, ductile iron has the greater yield strength (40 ksi). Cast steel, on the other hand, can only reach 36 ksi yield strength.
Ductile Iron (ASTM A536) vs Cast Steel (ASTM A27)
As the strength of ductile iron increases ductility decreases.
Cast ASTM A536 Ductile Iron | ||
Ultimate Tensile Strength (ksi) | Yield Strength (ksi) | Elongation (%) |
60 | 40 | 18 |
65 | 45 | 12 |
80 | 55 | 6 |
Cast Steel ASTM A27 | ||
Ultimate Tensile Strength (ksi) | Yield Strength (ksi) | Elongation (%) |
60 | 30 | 22 |
65 | 35 | 24 |
70 | 36 | 22 |
Ductile irons, in most cases, are defined by their tensile strength, yield strength and elongation. Design engineers will also want to know that a commonly accepted value of Poisson’s Ratio for ductile iron is 0.275.
The limit of proportionality is also important to design engineers. For ferritic grades (60-40-18) the ratio of proportional limit to 0.2% yield strength is typically 0.71. For pearlitic grades (80-55-06) the same ratio is typically 0.56.
Shock Absorption and Weldability
Ductile iron has superior shock absorption to steel. The average damping capacity for ductile iron is 6.6 times greater than SAE 1018 steel (reference – P. 435 ASM Cast Iron hand book).
Gray iron has a higher damping capacity than ductile iron. The presence of flake graphite causes gray iron to undergo non-elastic behaviour at very low stresses. Alternatively, steel is elastic up to its yield point, which gives steel a lower damping capacity than ductile iron.
Cast steel has greater weldability. To properly weld ductile iron it’s important to follow specialized weld procedures. If structural welding is required on castings, steel is likely a better choice.
Abrasion Resistance
Ductile iron has higher abrasion resistance than cast steel and is typically used in friction wear mechanisms e.g. engine crankshafts. Its superior abrasion resistance is due, in large part, to the high volume percentage of graphite which acts as a graphitic lubricant.
The fully pearlitic or martensitic ductile irons provide the best wear resistance. Neither mild steel nor ductile irons would be chosen solely for their resistance to abrasion. High chrome white irons are often the best material for solving any number of wear problems.
Read: To learn more about chrome white iron and abrasion resistance read this resource.
In abrasive wear mechanisms, austenitic ductile iron grades offer great wear resistance as well as improved strength. ADI grades of ductile iron are made by alloying the metal and heat treating.
There is a grade of austenitic ductile iron called carbidic austenitic ductile iron (CADI) that works well in abrasive applications when a designer needs to know the mechanical properties of the parts.
Corrosion Resistance
Ductile iron’s corrosion resistance is superior to unalloyed steel, and even highly alloyed steels in certain environments. Ductile iron’s corrosion resistance can be improved by understanding the corrosion mechanism and alloying the material appropriately.
Corrosion of ferrous alloys is a complex phenomenon, and the environment the casting is used in will greatly affect corrosion rates. There are several handbooks and surveys that will describe ductile iron’s behaviour in corrosive environments. The ductile ni-resists are specifically produced to be used at high temperatures. Their corrosion resistance is less than that of Cr-Ni stainless steels, and higher than that of unalloyed ductile iron.
Impact Resistance
Ductile iron’s impact properties are microstructure dependant. Ductile irons, in general, have good impact resistance. Type A395 ductile iron is fully ferritic. This is important as impact resistance depends on the degree of ferritization in the microstructure. Cast steel would be more consistent being a homogeneous microstructure.
The fracture toughness of good quality ferritic (60-40-18) ductile iron is excellent to temperatures as low as -62°C (-80°F). At this low temperature, the critical flaw size in ferritic ductile is 0.5 in. By sourcing castings from a reputable foundry, flaws of that size can be avoided. This means that the alloy can be thought of as being adequately tough enough to resist unstable crack propagation down to -62°C (-80°F).
Ductile iron, because of the increased strength and ductility is used in more engineered applications:
- Cable drums
- Frames
- Gear boxes
- Pumps
Benefits of ductile iron are as follows:
- Improved castability
- Lower costs
- Improved vibration damping
- Improved corrosion resistance
- Superior compressive yield strength
Applications typically made from steel include:
- Rail wheels
- Railroad truck frames
- Blowout preventers (B-O-P)
- Progressive cavity (PC) pump rotors
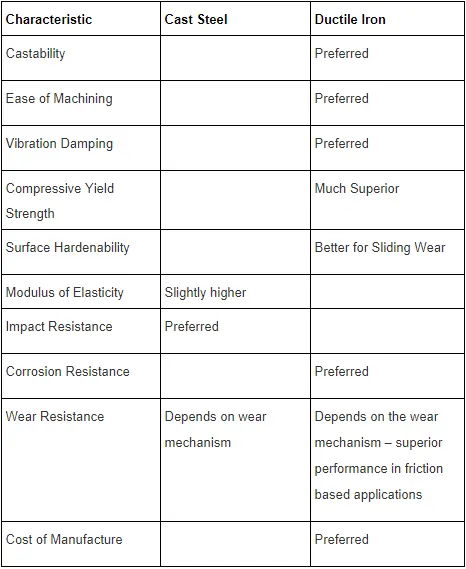
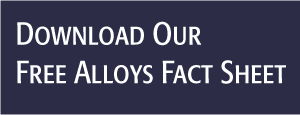