Chrome White Iron, ASTM A532, in the Fracking Industry
on June 1, 2021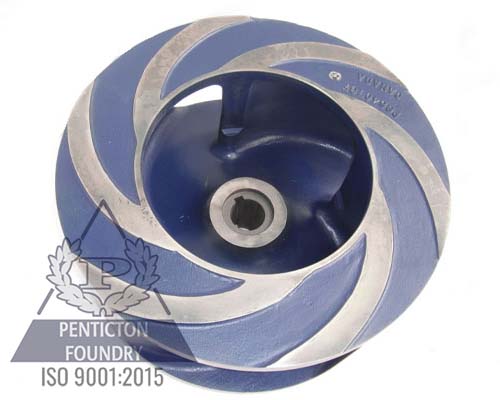
Because of its unique microstructure chrome white iron, ASTM A532, is particularly good in applications requiring gouging resistance. This is particularly true in industries such as mining, the Oil Sands and hydraulic fracturing.
Challenges in the Hydraulic Fracturing Industry
- Chemicals mixed with the proppant can be corrosive
- Thermal shock can be an issue with ceramic-lined parts
- For parts that are ceramic or CCO coated, it can difficult to determine the thickness and remaining wear life
- If ceramic-lined or weld overlay tubs delaminate this can cause catastrophic failures downstream
- The proppant can be angular, or sub-angular, and very abrasive
- The proppant can have high density and high velocity, which contributes to abrasive wear
- Ceramic or weld overlay tubs can be quite costly due to the man hours and materials required
Resource: Read “Chrome White Iron vs. Ceramic” for a more detailed comparison.
Chrome White Iron, ASTM A532, as a Solution
- Chrome white iron, ASTM A532, is able to handle the temperature changes associated with mixing and pumping proppants in many different environments. This is based on historical usage of chrome white iron in many different parts of North America
- Chrome white iron blender tubs can be measured with UT (ultrasonically tested) probes to determine their thickness (and remaining service-life). Parts that are ceramic or rubber coated cannot be ultrasonically tested from the outside. A unit like this would have to be shut down and opened to determine remaining wear life
- A solid chrome white iron, ASTM A532 blender tub, or components, will not delaminate like ceramic-lined components can. Delamination can be catastrophic if pieces travel downstream
- The chemistry and heat treatment of chrome white iron provide a matrix of martensite and carbides that provide excellent resistance to gouging abrasion of angular or sub-angular media
- Chrome white iron parts for the hydraulic fracturing industry can be provided in the fully machined and fully hardened state
- The casting process drastically reduces the man hours needed to make blender components. This results in lower costs compared to fabrications
Note: Penticton Foundry has developed a proprietary chrome white iron alloy called Granite 25 that is particularly corrosion resistant to many different compounds, including hydraulic fracturing proppant fluids.
Resource: To learn more about chrome white iron, check out our chrome white iron webpage.