High Chrome White Iron Vs. Ceramic
on November 3, 2020We’ve often done alloy comparison blogs, such as ductile iron vs. steel and ductile iron vs cast-iron. We’ve even looked at how chrome white iron stacks up against AR plate and CCO in abrasion resistant applications.
In this blog, we compare high chrome white iron, ASTM A532, with ceramic. For a quick summary, scroll down to the bottom of the blog and check out our chart.
Key Differences
- Resistance to Gouging Abrasion – Gouging abrasion involves large indents being formed in the surface, and is often coupled with material removal. High chrome white iron, ASTM A532, is much more resistant to gouging abrasion. This is because the tensile strength of chrome white iron is higher than that of ceramics used in abrasive applications.
- Impact – High chrome white iron has a greater impact resistance than the ceramics used in abrasive applications. ASTM A532 is especially useful if there might be tramp metal (like bucket teeth or grinding-ball shards) in the media.
- Processing Limits – Ceramics work well for very fine media in applications requiring abrasion resistance. When media becomes larger, however, chrome white iron is superior. This is because ceramics will typically break and spall away under the influence of larger media.
- Machinability – Chrome white iron can be machined as seen in this video. This allows creativity when solving wear challenges. Ceramics cannot be machined by traditional methods because they are too hard. They can be ground to shape with diamond-impregnated tooling, which is very expensive. If special shapes are required, ceramics can be cast to near-net shape.
- Designability – There are virtually no limits when designing with chrome white iron. It can be cast into the desired size and shape necessary to meet performance expectations for a given application. Ceramic can be cast to shape, but in most industrial applications it is used in tile-form (pre-existing shapes).
Read: Top 5 Design Mistakes of Chrome White Iron Castings to ensure that your castings perform as required. - Corrosion Resistance – Ceramics are chemically stable, and therefore more corrosion resistant than most metals and alloys. In most applications where chrome white iron is used, the failure mechanism is not corrosion, but erosion. High chrome white iron does possess a high level of corrosion resistance, and for most applications, the difference in corrosion resistance between these two materials is irrelevant.
- Hardness – Ceramics are hard due to their chemical bond at a molecular level. This strong bond is also what makes the ceramics fracture in a brittle fashion. For your application, if your only requirement is hardness, ceramic may be the better choice.
Read: To learn about the myths about chrome white iron and hardness read this blog. - Cost of Purchase – Often, installing ceramics into a wear application will be a very labour intensive operation. Tiles have to be installed onto the wall of a cyclone, or other vessel. This takes a lot of time, which can make the cost of purchase much more expensive than buying one casting made out of chrome white iron.
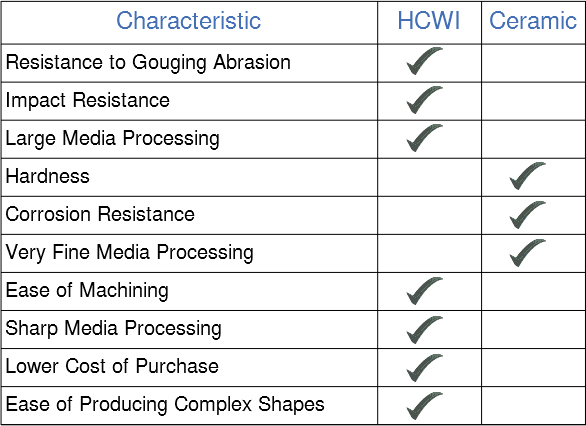
For more information on chrome white iron, check out our chrome white iron webpage.