Different Mill Liners and Alloys to Use
June 7, 2023
onMill Liners and Their Function
Industries such as mining, mineral processing, recycling, power generation and construction rely on grinding equipment. Liners, installed inside the equipment, eliminate wear and tear on the equipment itself, while at the same time helping to ensure grinding efficiency. While it is natural that liners will wear out during normal operation, they should be designed and manufactured to last until the next scheduled outage, as unplanned downtime is expensive. This makes selecting the appropriate alloy or material for the wear liner incredibly important.
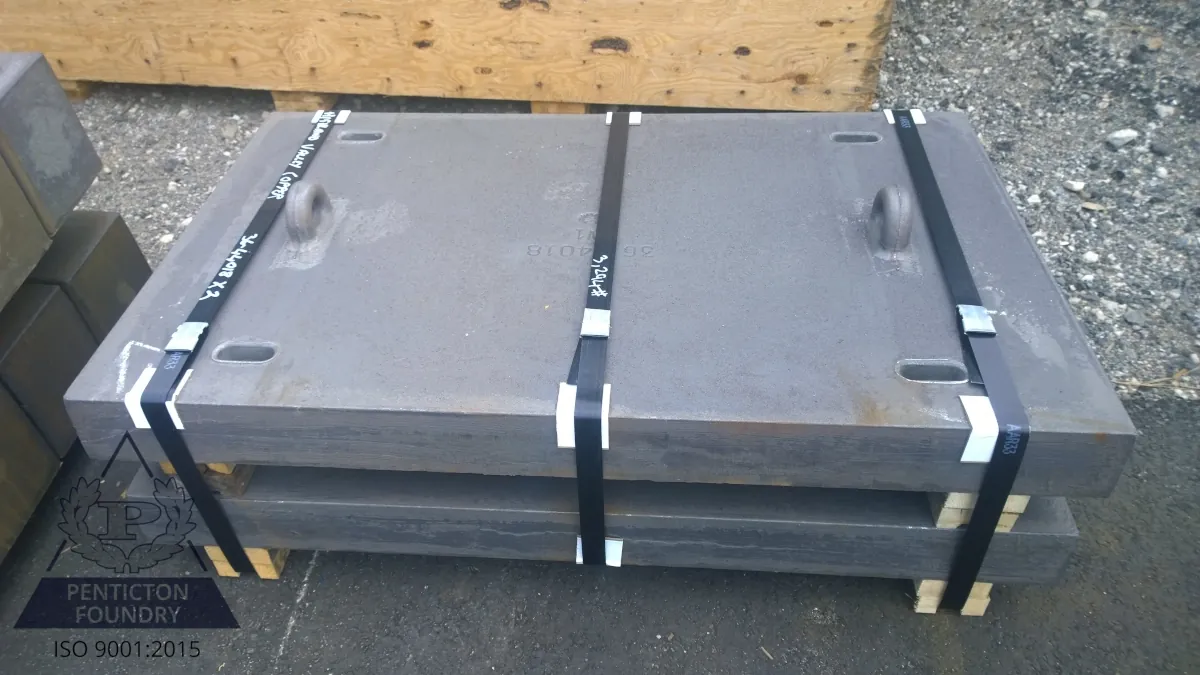
Different Types of Liners
1) Gyratory Crusher Liners
A gyratory crusher liner protects the mainframe and other parts of the gyratory crusher from wear and damage while the crusher is reducing ore to the proper size for further processing.
Possible alloys/materials:- Class III Type A high chrome white iron – specifically Tough 25 high chrome white iron – hardness maintained throughout, often the best choice for the lower row of gyratory liners, but not always the best choice for the top row (due to impact from truck unloading)
- Manganese steel – impact during use makes it tougher, but not as abrasion resistant as high chrome white iron. Often a good choice for the top row
- Alloy steel – more abrasion resistant than manganese steel, but not as tough. Less abrasion resistant than high chrome white iron, but tougher. If the ore being processed is exceptionally hard, it can be a good choice for the middle row
2) Apron Feed Liners (also known as loaf liners)
- Also called grizzlies, apron feeders feed quarry rock into a primary crusher
- The apron feeder liner protects the structure that is supporting it. The apron feeder is in place to allow media of the correct size to flow through for further processing
- Granite 25 high chrome white iron (ASTM A532 Class III Type A) – a common alloy that will perform very well in this application. The combination of martensitic microstructure and carbides make this alloy especially resistant to gouging abrasion. This is critical, as an apron feeder is subject to large, sharp rocks that are dropped though it
- 15-3 (ASTM A532 Class II Type B) – a lower Cr containing alloy that will, for an application like this, work well and can be less expensive, (depending on current raw material pricing). This alloy will perform as well as Granite25 in an apron feeder. It will not, however, provide the same level of corrosion resistance. This is most likely irrelevant in an apron feeder. Check with the foundry for current pricing to see which alloy is less expensive at the time of ordering
- Manganese steel – useful in an apron feeder if the process involves dumping lots of metal “tramp pieces” through the feeder
3) Trojan Horse Liners (also known as SAG infeed chute liners and feed chute liners)
- A trojan horse directs ore into a mill from a conveyor
- The liners protect the structure of the trojan horse and can be made to the exact geometry that is most advantageous for flow rate and maximum lifespan
- 20-1 (ASTM A532 Class II Type D) – a robust, medium-cost high chrome white iron that is useful when a thicker liner is needed
- Granite 25 high chrome white iron (ASTM A532 Class III Type A) – a work-horse alloy that may not have quite the same through hardness as the 20-1. For an added cost, this can be altered – just talk to your foundry
- AR plate – easy to buy in sheet form, easy to cut and easy to weld into place. Substantially less abrasion resistant than high chrome white iron, lasting a fraction of the time
Read: A feed chute liner (trojan horse liner) case study comparing chrome white iron and AR plate.
4) Trunnion Liners
- Trunnion liners fit around a mill trunnion to protect it from rotational wear, saving the integrity of the trunnion
- Bi-metal with steel backing and Granite 25 high chrome white iron (ASTM A532 Class III Type A) – The steel backing allows the liner to be fit into the bearing. The surface of the high chrome white iron can be machined to the size and surface finish that is required
- Ceramic-rubber liners – can be useful for this application due to high-speed sliding wear
Read: For more information comparing ceramic to chrome white iron, click here.
5) Surge Bin Liners
- A surge bin usually experiences the lowest amount of abrasive wear as material fills and flows out of the bin
- The feed chutes running in/out of the bin should be treated as above, but the liners inside the bin can usually be a softer material
- Granite 25 high chrome white iron (ASTM A532 Class III Type A) – an alloy that will work well for a thinner section size and also provide good corrosion resistance. Can be made thicker for the high-wear areas
- AR plate – sufficient for the very low wear points in the surge bin, like near the top of the walls
To optimize mill performance and reduce maintenance costs, it is critical to select the right alloys/materials for your liners. By doing so, mining and milling professionals can make informed decisions that maximize the lifespan of their wear liner.
Read: To learn more about chrome white iron, check out our chrome white iron webpage and our mining/crushing page.