Chrome White Iron and Potash Mining
on September 6, 2022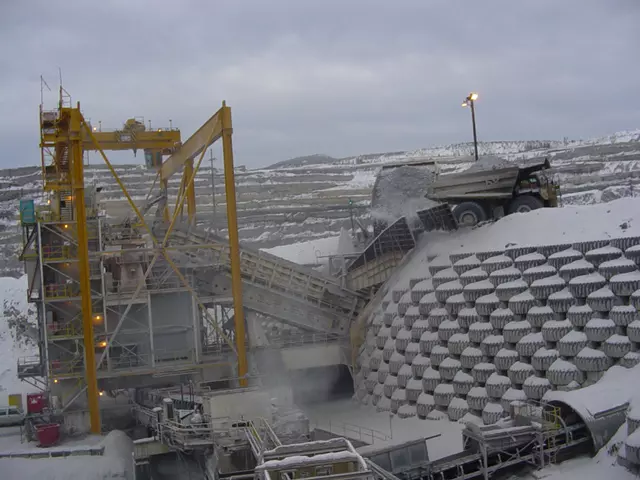
The chemical composition of high chrome white iron makes it an ideal material for use in an abrasive and corrosive environment like a potash mine. The variability of casting shape allows millwrights and engineers to use high chrome white iron castings in several applications. The significant increase in wear life leads to a decrease in downtime costs, and a more accurate shutdown schedule, ultimately saving money for the operator.
Most importantly, in spite of myths about hardness and brittleness, chrome white iron often outperforms other options like steel or weld overlay in wear applications for less money.
Read: This case study explores how chrome white iron outlasted AR 400 plate in an ore feed transfer chute.
Challenges in the Potash Mining Industry
There are four main steps in the potash mining process where wear is a concern:
- Continuous boring of the ore face
- Conveyance from the ore face to the main shaft
- Milling (crushing and grinding) of the ore after it is transported to the surface via the main shaft
- Sizing of the ore via a screening process
Challenges that result from the above steps are:
- The abrasive, corrosive media (ore) travels across many different surfaces, wearing down components
- The media makes directional changes, which increases the wear and tear in all the transitional components
- Unplanned downtime – expensive and can cause shipments to be delayed
- Planning shutdowns – changing worn components requires accuracy and diligence
- Worn parts can be challenging to replace
Why Using Chrome White Iron Makes Sense
- The chemistry of chrome white provides a material that forms a very thin Cr2O3 film on its surface. This will offer some protection from corrosion. Using an alloy with higher Cr will be even more beneficial.
Read: Check out this data sheet for an example of an alloy with higher Cr. - Chemistry and heat treatment of high chrome white iron can be manipulated to produce castings with a matrix of carbides and martensite that are extremely resilient in gouging abrasion applications.
- As the media is processed throughout the potash mining operation, transitions can impart sliding and/or impact onto wear parts. Shapes and thicknesses can be altered to provide longer life in problem areas.
Pro Tip: Castings do not have to conform to maximum thicknesses like overlays do. Read this blog to understand the top 5 mistakes to avoid when designing chrome white iron castings. - If slurry is being transported, pipe combining chrome white iron and steel will help solve wear challenges. Elbows, laterals, wyes, tees, reducers, etc. can all be produced with high chrome white iron in a pressure boundary. Corrosion and abrasion wear rates, in a high-pressure system, can be reduced. This will increase uptime, and allow planners to more accurately schedule shutdowns
- Installation of chrome white castings is relatively easy. A foundry’s engineers can work in partnership with a mine’s engineers and millwrights to design the system that is most effective
Read: To learn more about chrome white iron, check out our chrome white iron webpage. It contains details about each chrome white iron alloy, as well as links to data sheets with additional information.